Interview réalisée par le pôle TEAM2
« La fabrication additive ne génère pas de déchets, pas de copeau. » Partant de ce constat, Patrick Gaspard décide de réorienter son activité de fabrication additive en réemployant des matériaux recyclés. C’était donc une évidence pour lui de s’installer dans la pépinière d’éco-entreprises de Loos-en-Gohelle. Il revient avec nous sur l’origine de R3D et les projets de développement futurs de cette jeune entreprise prometteuse.
A l’origine l’activité de R3D n’était pas axée sur l’économie circulaire…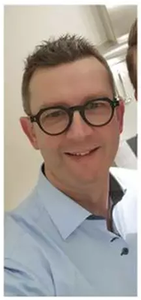
Je suis issu du monde automobile où je travaillais pour les constructeurs et carrossiers, dans l’aménagement des véhicules utilitaires. Mais j’ai souhaité aller plus loin dans l’économie circulaire pour la fabrication additive. Depuis longtemps, l’amidon de maïs – une matière biodégradable – était utilisé. Mais, face à la réduction des ressources à venir, j’ai souhaité aller plus loin dans l’économie circulaire et trouver des matières recyclables pour en faire de nouveaux objets.
Aujourd’hui, quels types de matières entrantes utilisez-vous ?
J’utilise du fil fabriqué par extrusion à partir de matière recyclée ou d’amidon de céréales, ou encore de la matière issue des hydrocarbures qui est recyclable une dizaine de fois. Avec un partenaire, je suis sur un projet de création de matière à partir d’un mélange de plastiques « post-consumer » issus des poubelles de tri et de déchets industriels afin de charger la matière pour pouvoir l’imprimer directement. Mon idée a également une finalité éducative en disant aux populations « Triez bien vos déchets et vous pourrez imprimer des objets pour votre ville. »
Quels types d’objets sortent aujourd’hui de vos machines ?
Je fais surtout des pièces destinées au secteur automobile, ainsi que pour l’industrie de l’ameublement, la fabrication de drones et l’environnement. Par exemple, je fabrique des grilles de filtration des eaux pour des dalles extérieures qui ont aussi l’avantage de faciliter le passage des fauteuils roulants. Et pour les drones, je réalise des accessoires sur-mesures. Je réalise aussi des gabarits pour aider la production industrielle ainsi que des prototypes. En fait, nous intervenons dès l’amont de la production industrielle grâce à la CAO pour pouvoir sortir des prototypes très rapidement, effectuer des mises au point de manière très réactive, puis nous pouvons produire en petite série pour les clients.
Quel est le processus de réalisation d’une pièce ?
Notre vraie valeur ajoutée se situe en amont du processus. Concrètement, un client nous appelle avec une problématique – il ne donne généralement pas de cahier des charges – et nous revenons trois jours plus tard avec la solution de pièce ayant la forme et la matière adéquate. Et souvent nous poursuivons avec la production des pièces en petite série jusqu’à 500/600 pièces, mais nous évoluons vers des volumes plus importants car les machines vont de plus en plus vite.
En matière de coût de fabrication, l’impression 3D est-elle compétitive ?
Il y a un seuil à calculer avant de choisir entre l’impression 3D et une production classique. En fabrication additive, l’investissement de départ est nul car il n’y a pas d’outillage à acheter. Mais le prix pièce est plus élevé car la fabrication est plus longue. D’ailleurs, nous calculons ces seuils en fonction des quantités de pièce et alertons nos clients dès que l’investissement dans un outillage devient pertinent. Puis, nous les accompagnons en ingénierie afin de choisir la meilleure solution.
Etes-vous nombreux dans votre domaine d’activité ?
L’impression 3D existe depuis 25 ans. D’autres sociétés issues du monde du prototype se sont équipées au fur et à mesure pour la fabrication additive. Elles ont réalisé qu’il s’agissait également d’un moyen industriel et se sont lancées sur ce créneau-là. Mais toutes n’utilisent pas de matériaux recyclés malheureusement. C’est notre marque de fabrique et nos clients y sont de plus en plus sensibles.
Rencontrez-vous parfois des réticences face aux matières recyclées ?
Cela arrive et la première des craintes que les clients expriment est celle d’une qualité moindre due aux matériaux recyclés. Mais, comme nous fournissons très rapidement un échantillon, ils peuvent regarder, toucher et même tester. Et puis, il est inutile de demander plus de résistance à ces pièces qu’à celles issues d’une fabrication classique. On est équivalent voire plus résistant car nous réalisons des calculs afin de préconiser les bonnes formes et la bonne manière de les remplir. La qualité tient essentiellement à la manière dont sont conçues les pièces.
Dans le secteur de l’économie circulaire, quels enjeux avez-vous identifiés pour l’avenir ?
Le véritable enjeu en ce qui concerne le plastique est d’arriver à un niveau de réemploi qui dépasse largement celui du plastique issu des hydrocarbures. Pour cela, il faut que toute la filière de recyclage – collecte, réemploi et réutilisation d’objets – se mette en place de façon industrielle en offrant des coûts aussi compétitifs qu’un produit vierge.
Comment avez-vous connu le Pôle TEAM2 ?
J’ai monté un dossier « Industrie du Futur » et un « Diagnostic Innovation » pour lesquels TEAM2 m’a permis d’entrer en relation avec les bons interlocuteurs de la Région. J’ai donc pu obtenir des financements grâce à l’appui du pôle.
R3D est une toute jeune entreprise, quels sont vos objectifs de développement ?
Le projet d’entreprise que j’ai présenté à la Région Hauts-de-France et à la BPI est axé sur la démultiplication des moyens de production, en partant sur des moyens plus gros. Aujourd’hui, nous avons un parc machines de 8 imprimantes à dépôt de fil plastique et nous souhaitons passer sur de très grosses machines pour imprimer des pièces de grande taille et en grande quantité. En effet, si l’on veut réutiliser de la matière plastique en volume, il faut créer des grosses pièces pour que cela soit rentable. Ce développement nous amène à embaucher une personne d’ici à la fin de l’année, et l’équipe devrait compter une dizaine de personnes à horizon 5 ans. Puis nous continuerons crescendo les années suivantes. Enfin, nous déménagerons certainement dès l’année prochaine pour avoir plus d’espace. Concernant notre activité, nous envisageons de créer nos propres produits pour les vendre en direct en complément des services actuellement offerts à nos clients.
Au niveau de votre territoire d’intervention, quel périmètre visez-vous ?
Aujourd’hui, je suis sur un périmètre national. A terme, je souhaiterais implanter localement la production, à proximité des gisements de déchets. Dans les Hauts-de-France, nous avons des plastiques issus de l’industrie automobile, des déchets de verre, des laitiers des hauts fourneaux alors que dans d’autres régions, nous aurons des plastiques sourcés différemment à mélanger à d’autres déchets industriels locaux. Notre idée est donc de s’adapter à la typologie locale avec l’implantation d’un site pour la récupération des déchets et la fabrication. Nous nous tournerons aussi vers les pays limitrophes des régions où nous serons implantés. Nous avons des objectifs ambitieux mais je souhaite construire cette entreprise sur des fondations solides pour la pérenniser.
Vous avez adapté votre production pendant la crise sanitaire…
Pendant le confinement nous nous sommes lancés dans la fabrication de visières de protection et cela nous a permis de passer le cap du confinement. Et aujourd’hui je distribue des attache-élastiques pour maintenir le masque sans avoir mal aux oreilles. J’ai commencé par les donner à mes clients et finalement on m’en a commandé plusieurs séries.
Quels sont vos projets pour la fin de l’année 2020 ?
Nous ne manquons pas de projets et nos machines tournent en continu, mais nous aimerions avoir plus de visibilité sur la demande afin de pouvoir établir des plans de production. On nous annonce un regain de production dans l’industrie automobile pour le 2ème trimestre 2021 donc cela est encourageant. Et puis l’économie circulaire est un secteur d’avenir et je suis ravi d’avoir rejoint cet univers passionnant !
Amandine Clémençon pour TEAM2
L’impression 3D, oui on y croit.